Maximizing Efficiency: Integrating Pneumatic and Lifting Equipment in Mining
In the mining industry, efficiency is crucial for maximizing productivity while minimizing costs. www.balkancorex.rs One effective strategy for achieving this is the integration of pneumatic and lifting equipment. By leveraging the strengths of both technologies, mining operations can enhance workflow, improve safety, and optimize resource management. This article explores the benefits and best practices for integrating pneumatic and lifting equipment in mining.
The Role of Pneumatic Equipment in Mining
Pneumatic equipment, which operates using compressed air, plays a vital role in various mining applications. It is commonly used for:
- Drilling: Pneumatic drills provide high power-to-weight ratios, allowing for efficient penetration of rock and soil.
- Material Handling: Pneumatic conveyors facilitate the transport of bulk materials, reducing manual handling and increasing speed.
- Rock Fragmentation: Air-powered tools, such as jackhammers, are effective for breaking up rock with minimal vibration, preserving surrounding structures.
The lightweight nature of pneumatic tools allows for greater maneuverability and reduced operator fatigue, contributing to overall productivity.
The Importance of Lifting Equipment
Lifting equipment, including cranes, hoists, and forklifts, is essential in mining for handling heavy materials and machinery. Key benefits include:
- Safety: Modern lifting equipment is designed with advanced safety features that reduce the risk of accidents when moving heavy loads.
- Efficiency: The right lifting equipment can streamline operations, reducing the time and effort required to transport materials across the site.
- Versatility: Many lifting systems can be adapted for various tasks, making them valuable assets in diverse mining operations.
Benefits of Integration
Integrating pneumatic and lifting equipment can lead to significant efficiency gains in mining operations. Here are some key advantages:
1. Streamlined Operations
By combining pneumatic systems with lifting equipment, mining operations can create seamless workflows. For instance, pneumatic conveyors can transport materials directly to the lifting equipment, minimizing the need for additional handling. This integration reduces downtime and enhances overall productivity.
2. Improved Safety
Integrating these systems can enhance safety protocols. Pneumatic tools often reduce the physical strain on workers, while modern lifting equipment includes safety features such as overload protection and automatic shut-off systems. Together, they create a safer working environment by minimizing manual handling and the risk of accidents associated with heavy lifting.
3. Enhanced Equipment Utilization
Integrating pneumatic and lifting systems allows for better utilization of equipment. For example, pneumatic tools can be powered directly from the same compressed air system used for lifting equipment, reducing energy consumption and ensuring that resources are used efficiently.
4. Cost Savings
The combination of these technologies can lead to significant cost savings. Increased efficiency results in reduced labor costs and downtime. Additionally, by optimizing equipment usage and energy consumption, mining operations can lower their operational expenses.
Best Practices for Integration
To effectively integrate pneumatic and lifting equipment in mining operations, consider the following best practices:
1. Conduct a Thorough Assessment
Before integration, assess the specific needs of your operation. Identify areas where pneumatic tools and lifting equipment can complement each other. This assessment should consider factors such as workload, site layout, and the types of materials handled.
2. Invest in Compatible Equipment
Select pneumatic and lifting equipment that is compatible and can work together seamlessly. This may involve investing in modern systems that feature advanced controls and automation capabilities, ensuring they can communicate effectively.
3. Train Personnel
Proper training is essential for maximizing the benefits of integrated systems. Ensure that operators are skilled in using both pneumatic tools and lifting equipment. This training should include safety protocols and best practices for operating the equipment in tandem.
4. Implement Regular Maintenance
Regular maintenance is crucial to ensure both pneumatic and lifting equipment operate at peak efficiency. Schedule routine inspections and servicing to prevent breakdowns and extend the lifespan of your equipment.
5. Monitor Performance
Establish key performance indicators (KPIs) to monitor the effectiveness of the integrated systems. Analyze data to identify areas for improvement and make adjustments as necessary to enhance efficiency.
Conclusion
Integrating pneumatic and lifting equipment in mining operations offers a pathway to maximizing efficiency and productivity. www.balkancorex.rs By streamlining processes, improving safety, and reducing costs, mining companies can gain a competitive edge in a challenging industry. As technology continues to evolve, the potential for further integration and innovation remains significant, paving the way for a more efficient future in mining.
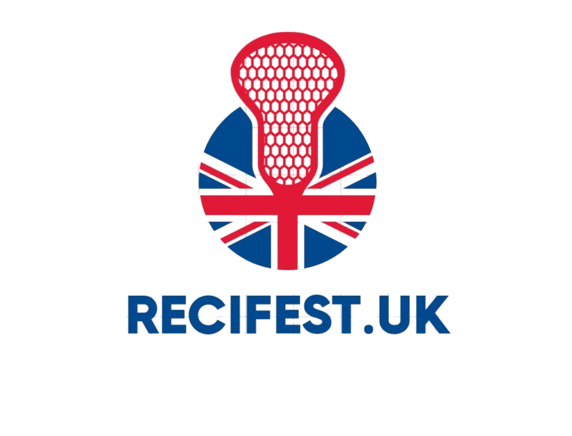